THE LUBRICATION SYSTEM
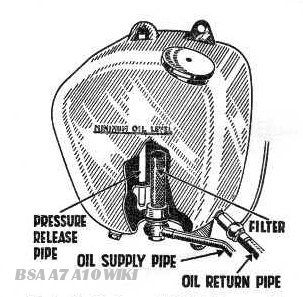
The engine lubrication system is of the dry sump type operated by a double gear pump situated in the bottom of the timing case. All oilways are internal except for the supply and return pipes to the tank and the feed to the rocker spindles. The oil flows from the tank - through a filter in the tank - to the supply portion of the pump, which delivers it past an automatic valve to the timing side main bearing, and thence to the hollow crankshaft and the big-end bearings.
Oil pressure is maintained at the big-ends by the pressure release valve A (Fig. A2). When the pressure in the system exceeds 50/60 lbs. per square inch, this valve opens and allows surplus oil to be passed into the bottom of the timing case,
On A10 machines after Engine No. ZA10-4712, and A7 machines after Engine No. AA7-101, the crankcase has been modified to provide an additional oil supply to the cylinders. The oil by-passed by the pressure release valve is now fed through drilled oilways to the camshaft trough, and is then directed on the cylinder walls (Fig A2). A small bleed hole also provides additional lubrication to the timing gear.
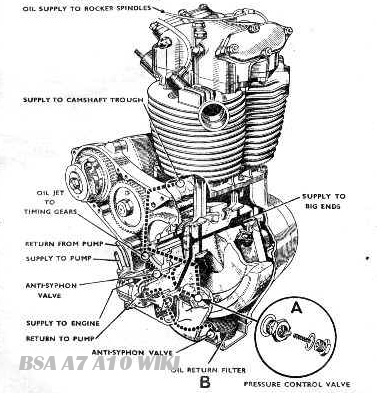
After lubricating the big-ends and circulating through the engine in the form of mist, the oil drains down through a filter in the bottom of the crankcase.
From there it is drawn through a non-return valve by the return portion of the pump (large gear set) and delivered up the return pipe to the tank.
To check the flow of oil in the lubricating system, remove the tank filler cap while the engine is running Oil should be seen issuing from the return pipe from the crankcase.
Any restriction in the pressure release pipe in the tank will cause an increase in pressure inside the oil tank, and will result in leakage of oil at the filler cap. This can be remedied by inserting a piece of flexible wire into the outer end of the pipe to clear any obstruction.
Lubrication Of The Rockers
On machines before Engine No. XA7-450, all the valves and rockers are lubricated by oil mist from the crankcase.
On machines from Engine No. XA7-450, and before YA7-3402 oil is fed to the exhaust rocker spindle only.
On all A7 engines after YA7-3402 and on all A10 machines oil is fed to both the inlet and exhaust rockers and lubricates the remainder of the valve gear in the form of oil mist.
The rocker box oil supply is obtained from a union to the point where the oil return pipe is attached to the oil tank.
The Oil Pressure Release Valve
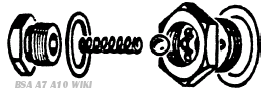
This valve should open when the pressure in the supply system reaches 50/60 lbs. per square inch The valve ball is of 5/16in. diameter. Remove the valve when oil changing, clean it and ensure that it is operating freely. See Service Sheet 203 for further details of dismantling,
Oil Change
In case of new or re-conditioned engines, the oil should be drained and renewed after the first 280 miles, and again after 500 miles. Then periodically every 2,000 miles.
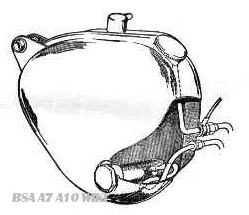
Drain the oil tank and the sump, preferably when the engine is hot. by removing the drain plug and the banjo with the filter at the bottom of the tank. Also the drain plug and the cover with the filter B on the bottom of the crankcase. Clean by washing in petrol. Before replacing make sure that the parts are quite dry.
On Swinging Arm models the construction of the oil tank is slightly different, but the system of oil flow is the same. The oil filter is attached to the hexagon nut in the side of the tank and unscrewing it will provide access to the filter without disturbing the oil supply pipes.