GENERATORS - MODELS E3L, E3LM AND E3N
All Models except Dl, C10L, C11G, C12, C15 & B group fitted with alternator
GENERAL
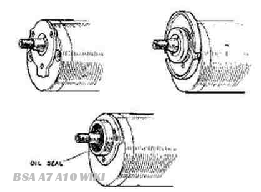
Fig.1 Various drive-end bearing retaining plates
The generator is a shunt-wound two pole machine arranged to work In conjunction with a regulator unit (see SECTION L-3) to give an output which is dependent on the state of charge of the battery and the loading of the electrical equipment In use. When the battery Is in a low state of charge, the generator gives a high output, whereas if the battery Is fully charged the generator gives only a trickle charge to keep the battery in a good condition without overcharging. In addition, an increase of output Is given to balance the current taken by the lamps when in use. Models E3L and E3LM are similar In construction and both have a 60 watt output. The constructional difference between the two models Is In the shape of the drive-end bearing retaining plate; Model E3L Is designed to fit on to the engine crankcase and Model E3LM to be the upper portion of the 'Magdyno'.
Model E3N is identical In diameter and construction to the two previously mentioned models, but differs In overall length and output. The output Is 45 watts and the overall length is 1/4 less than that of Models E3L and E3LM.
TEST DATA
Models
|
Cutting in Speed(generator cold)
|
Output Test
|
Field Resistance
|
Brush Spring Tension
|
E3L
E3LM
|
1050-1200 r.p.m. at 7 volts
|
8.5 amps. at 1850-2000 r.p.m. at 7 volts *
|
2.8 ohms
|
16-20 oz.
|
E3N
|
1250-1500 r.p.m. at 7 volts
|
5 amps at 2100-2300 r.p.m. at 7 volts, **
|
3.2 ohms
|
16-20oz.
|
ROUTINE MAINTENANCE
Lubrication
No lubrication is necessary as the ball bearings are packed with H.M.P. grease which will last until the machine Is taken down for a general overhaul, when the bearings should be repacked. Thin lubricating oil. if allowed to reach the bearings, will soften the grease and eventually cause the bearings to run hot.
Inspection of Commutator and Brushgear
About once every six months remove the cover band for inspection of commutator and brushes. The brushes are held In contact with the commutator by means of springs. Move each brush to see that it is free to slide in its holder; (if it sticks, remove It and clean with a cloth moistened with petrol. Care must be taken to replace the brushes In their original positions, otherwise they will not 'bed' properly on the commutator. If. after long service, the brushes have become worn to such an extent that the brush flexible is exposed on the running face, or If the brushes do not make good contact with the commutator, they must be replaced by genuine Lucas brushes. The commutator should be free from any trace of oil or dirt and should have a highly polished appearance. Clean a dirty or blackened commutator by pressing a fine dry cloth against it while the engine is slowly turned over by means of the kick starter crank. (It Is an advantage to remove the sparking plug before doing this.) If the commutator is very dirty, moisten the cloth wilh petrol.
SERVICING
Testing in position to locate fault in charging circuit
In the event of a fault In the charging circuit, adopt the following procedure to locate the cause of trouble.
(I) Check that the generator and regulator unit are connected correctly. The generator terminal 'D' should be connected to the regulator unit terminal 'D' and generator terminal 'F' to regulator unit terminal 'F'.
(II) Remove the cables from the generator terminals
'D' and 'F' and connect the two terminals with a short length of wire.
(Ill) Start the engine and set to run at normal idling speed.
(IV) Connect the negative lead of a moving coil voltmeter. calibrated 0—10 volts, to one of the generator terminals and connect the positive lead to a good earthing point on the generator yoke or engine. Reverse voltmeter connections on negative earth machines.
(V) Gradually increase the engine speed, when the voltmeter reading should rise rapidly and without fluctuation. Do not allow the voltmeter reading to rise above 10 volts and do not race the engine in an attempt to Increase the voltage. It Is sufficient to run the generator up to a speed of 1,000 r.p.m. If there is no reading, check the brush gear, as described in (VI)below. If there is a low reading of approximately 1/2 volt, the field winding may be at fault (see Para. 4 (d)). If there is a reading of approximately 11/2 to 2 volts. the armature winding may be at fault (see Para. 4 (e).
(VI) Remove the cover band and examine the brushes and commutator. Hold back each of the brush springs and move the brush by pulling gently on Its flexible connector. If the movement is sluggish, remove the brush from its holder and ease the sides by lightly polishing on a smooth file. Always replace brushes in their original posliions. If the brushes are worn so that they do not bear on the commutaror. or If the brush flexible is exposed on the running face, new brushes must be fitted.
Test the brush spring tension with a spring scale. The correct tension is 16 - 20 oz. and new springs must be fitted if the tension is low.
If the commutator is blackened or dirty, clean It by holding a petrol moistened cloth against It while the engine is turned slowly by means of the kick start (with sparking plug removed).
Re-test the generator as in (v) above. If there is still no reading on the voltmeter, there is an internal fault and the complete unit if a spare is available, should be replaced. Otherwise the unit must be dismantled (see Para. 4 (b) for Internal examination.
(Vll) If the generator Is In good order, restore the original connections. Connect regulator unit terminal 'D' to generator terminal 'D', and regulator terminal 'F' to generator terminal 'F'. Proceed to test the regulator as described in SECTION L-3 Part A.
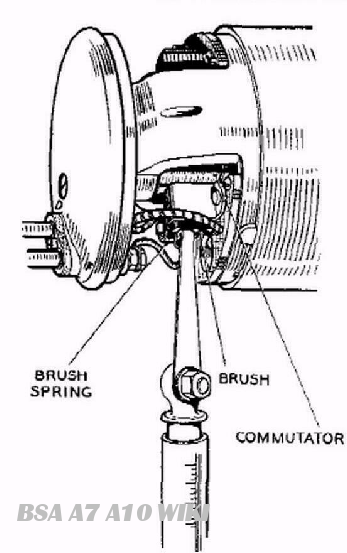
Fig. 3 testing brush spring tension
To Dismantle
Remove the generator from the motorcycle. To detach the generator from a Magdyno, unscrew the hexagon-headed nut from the driving end cover and slacken the screws securing the band clip.
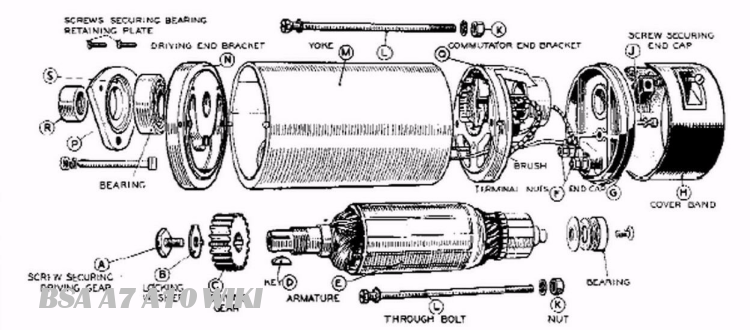
Fig. 3 Dismantled view of Model E3LM
Proceed to dismantle as follows:—
(I) On models E3L and E3N, remove the securing nut from the drive end of the shaft, and withdraw the gear with the aid of an extractor. On model E3LM, bend back the tag on the washer 'B' locking the screw
'A'. Remove this screw, withdraw the gear 'C' from the shaft with the aid of an extractor and remove the key(s) 'D' from the shaft.
(II) Remove the cover band 'H'. hold back the brush springs and lift the brushes from their holders.
(III) Take out the screw 'I' with spring washer, from the centre of the black moulded end cap 'G'. Draw the cap away from the end bracket, take off terminal nuts 'F', and spring washers, and lift the connections off the terminals.
(IV) Unscrew and remove from the drive end bracket, the two through bolts 'L' securing the drive end bracket 'N' and commutator end bracket 'Q* to the yoke 'M'. Hold the nuts 'K' at the commutator end while unscrewing the bolts, and take care not to lose the nuts.
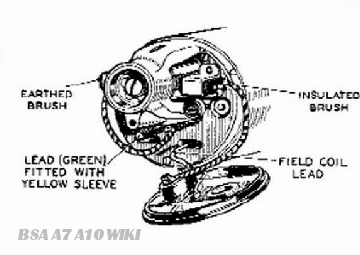
Fig.5 Generator connections
(v) Draw the drive end bracket complete with armature 'E' out of the yoke,
(VI) Remove the nut 'R' and press the armature out of the drive end bracket by means of a hand press. When removing the armature from an E3L generator fitted with a rubber oil seal 'S' take great care not to damage the sealing lip.
(VII) Remove the bearing retaining plate 'P' from the drive end bracket (secured by three screws on E3L and E3N models, or two screws and lone threaded bolt on E3LM models).
(VIII) Take out the screw securing the green field coil lead with the yellow sleeve to commutator end bracket and remove the end bracket 'Q' withdrawing the connectors through the slot In the Insulating plate.
(IX) Unscrew ihe three screws securing the insulating plate to the commutator end bracket and remove the plate complete with brushgear.
Commutator
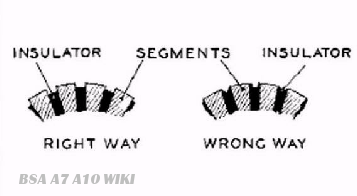
Fig. 4 Method of Under-cutting commutator Insulation
Examine the commutator. If it Is in good condition. It will be smooth and free from pits or burned spots. Clean with a petrol-moistened cloth. If this is ineffective. carefully polish with a strip of very fine glasspaper while rotating the armature. To remedy a badly worn commutator, mount the armature with or without the drive end bracket in a lathe, rotate at high speed and take a light cut with a very sharp tool. Do not remove more metal than is necessary. Polish the commutator with very fine glass-paper.
Undercut the insulation between the segments to a depth of 1/32" with a hacksaw blade ground down until it is only slightly thicker than the insulation.
Field Coil
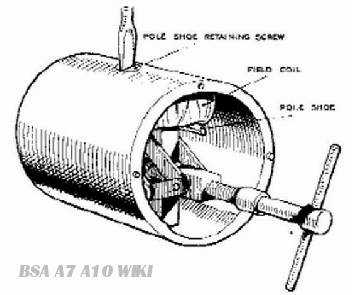
Fig .6 Pole shoe expander
Measure the resistance of the field winding by means of an ohm meter. If this Is not available, connect a 6 -volt D.C. supply with an ammeter In series across the coll. The ammeter reading should be approximately 2.1 amps. for models E3L and E3LM and 1.8 amps for E3N. No reading on the ammeter indicates an open cjrculi in the field winding.
To check For an earthed coil. connect a mains test lamp between one end of the coil and the yoke. If the bulb lights there is an earth between coll and yoke.
In either case. unless a replacement generator Is available, the field coil must be replaced, but this should only be attempted if a wheel-operated screwdriver and pole shoe expander are at hand. the latter being especially necessary to ensure that there will be no airgap between the pole shoe and the inner face of the yoke.
To replace the field coll, proceed as follows:-
(I) Unscrew the pole shoe retaining screws) (Fig. 6) by means of the wheel-operated screwdriver.
(II) Draw the pole shoe and field coll out of the yoke and lift off the coil.
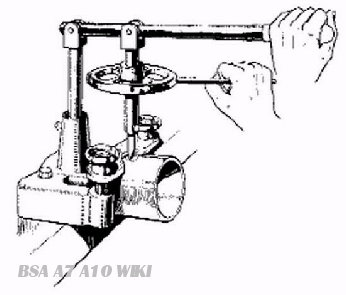
Fig. 7 Wheel-operated screwdriver
(III) Fit the new field coll over the pole shoe and place it in position inside the yoke. Take care to ensure that the taping of the field coil Is not trapped between the pole shoe and the yoke.
(IV) Locate the pole shoe and field coil by lightly tightening the fixing screw(s), insert the pole shoe expander, open to it< fullest extent and tighten the acrew(s). Remove the expander and give the screw(s) a final tightening with the wheel-operated screwdriver Lock the screw(s) in position by caulking, that is, by tapping some of the metal of the yoke into the slot in the head of the screw(s).
Armature
The testing of the armature winding requires the use of a voltdrop test or a growler, if these are not available. the armature shouJd be checked by substitution. No attempt should be made to machine che armature core or to true a distorted armature shaft.
Bearings
Ball bearings are fitted to both the commutator and drive end brackets. When the bearings become worn to such an extent that they allow side movement of the armature shaft, they must be replaced. To replace the ball bearing at the commutator end. proceed as follows:—
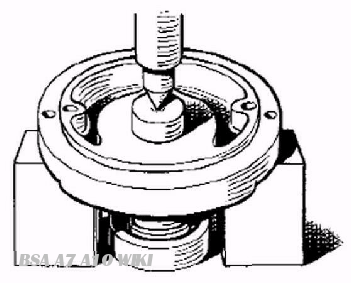
Fig. 8 Removing the ball race
(I) Remove the screw from che end of the armature shaft and using a calliper type extractor, draw the bearing off the shaft.
(lI) Wipe out the bearing housing and pack the new bearing with H.M.P. grease.
(III) Position the bearing on the end of the shaft and press it souarely home, applying pressure on the Inner journal of the bearing.
To replace the ball bearing at the drive end. proceed as follows:
(I) Remove the bearing retaining plate from the drive end bracket as previously described.
(II) Press the bearing out of the end bracket, using a metal drift locating on the inner journal of the bearing. Wipe out the bearing housing and pack the new bearing with H.M.P. grease.
(iv) Position the bearing in its housing and press it squarely home. applying pressure on the outer journal of the bearing.
Reassembly
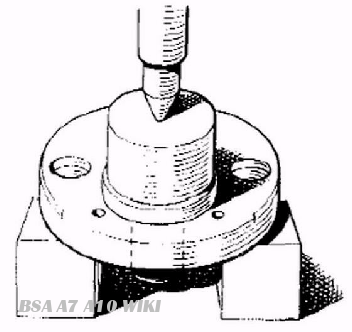
Fig.9 Replacing the ball race
In the main. the reassembly of the generator is a reversal of the operations described In paragraph 4 (b), bearing in mind the following points:—
(I) The field coil lead fitted with the short length of yellow tubing must be connected together with the eyelet of the earthed brush to the commutator end bracket by means of the screw provided.
(II) The second field coil lead must be connected to terminal 'F' on the moulded cap.
(III) The unearthed brush flexible lead must be connected direct to terminal 'D' on the moulded end cap.
(IV) Take care to refit cover band in original position and make sure that the securing screw, when of flush-fitting pattern, does not short on brushgear.
(V) On E3L generators with oil seal, ensure that no damage has been caused to the seal, otherwise replacement mu»t be made. To remove the oil seal from the bearing retaining plate, use a metal drift locating on the outer edge of the rubber seal. Insert a new seal using a mandrel to press it squarely home.
GENERATOR POLARITY
All replacement motor cycle generators are dispatched from the Works suitable for Immediate use on positive earth systems. If the negative terminal of the battery Is earthed on the machine for which the replacement generator is intended, It will be necessary to re-polarize the generator before use to make it suitable for negative earth.
Similarly, if a generator has been Incorrectly connected on the motorcycle and its polarity has become reversed, then It must be re-polarized.
To do this, fit the generator to the motor cycle but do not at this stage connect the cables to the D and F terminals. Temporarily connect a length of wire to the battery positive terminal and hold the other end
of this wire In contact with generator terminal F for a few seconds only. This serves to re-polarize (he generator: the temporary connection can now be removed and the original cables connected to D and F terminals.
The practice of closing the cut-out points to reverse the generator polarity is not recommended as this method allows a high Initial surge of current from the battery to pass through the armature, which can damage the windings. Insulation, etc, and result in a decreased service life of the machine.
Generally speaking, the majority of motor-cycles manufactured up to and including 1951 had the negative terminal of the battery connected to the frame. The majority of machines In current production have the positive terminal earthed.